Our Blogs
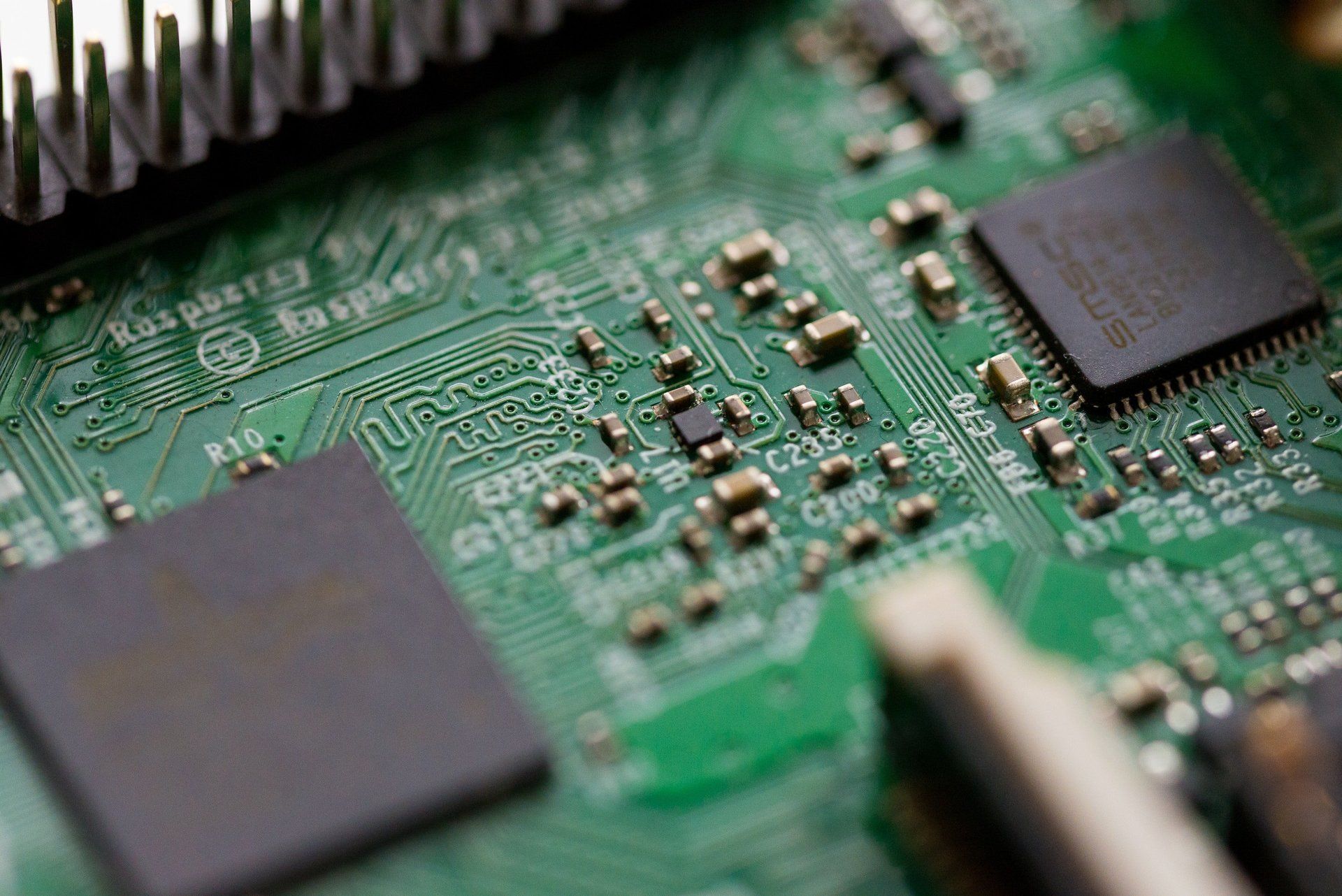
In today’s fast-paced metal fabrication industry, staying competitive means modernizing equipment without incurring the steep costs of full machine replacements. CNC Retrofits are emerging as a cost-effective solution to revitalize aging machinery while ensuring that production remains efficient, precise, and adaptable to modern requirements.
Understanding CNC Retrofits
CNC retrofits involve upgrading older machines with PC-based control systems that provide state-of-the-art interfaces and real-time monitoring capabilities. This process allows fabricators to:
- Integrate Modern Software: Replace outdated control panels with intuitive software solutions like Bend Wizard, Shear Wizard, and Punch Wizard.
- Improve Operational Precision: Benefit from enhanced control features that improve accuracy in metal fabrication processes.
- Extend Machine Lifespan: Maximize the value of existing machinery by updating only the control system rather than purchasing entirely new equipment.
Why Upgrading Matters
Many metal fabricators face challenges with obsolete CNC systems, including limited functionality and increased downtime. Modernizing these systems offers several benefits:
- Enhanced Production Efficiency: New control systems streamline processes and reduce cycle times.
- Reduced Maintenance Costs: Modern interfaces simplify troubleshooting and repair, helping to lower long-term maintenance expenses.
- Competitive Advantage: Upgraded machines are better equipped to handle the precision and complexity demanded by modern fabrication techniques.
Product Spotlight: Press Kit and Punch Kit
At PC Controls, the focus is on providing tailored retrofit solutions:
- Press Kit: Designed specifically for press brakes and related machinery, the Press Kit integrates modern PC-based controls with existing hardware. This upgrade enhances the machine’s performance, ensuring smoother operation and improved precision.
- Punch Kit: Ideal for retrofitting single punches and other forming equipment, the Punch Kit offers robust control solutions that bring advanced diagnostics and real-time feedback to traditional machinery.
These products are part of a broader suite of offerings that not only improve machine functionality but also extend the life of the equipment, ensuring that fabricators can continue to produce high-quality work without interruption.
Real-World Applications
Many companies are turning to CNC retrofits as a way to solve common industry challenges:
- Reducing Downtime: Upgraded controls allow for faster diagnostics and quicker repairs, minimizing production interruptions.
- Improving Product Quality: Enhanced precision means fewer errors and less material waste, resulting in better end products.
- Cost Savings: By updating only the control systems, companies avoid the significant capital expense associated with purchasing brand-new machinery.
Tips for a Successful Retrofit
Implementing a CNC retrofit project requires careful planning:
- Evaluate Your Needs: Consider which parts of your machine require the most attention. Focus on areas that directly impact productivity and quality.
- Plan for Integration: Ensure that new controls can be seamlessly integrated with your existing equipment. This might involve minor modifications or additional support services.
- Train Your Team: Modern systems come with advanced features. Investing in proper training will maximize the benefits of the retrofit and ensure your staff can leverage all available functionalities.
Embracing CNC Retrofits is a strategic move that can significantly boost operational efficiency, reduce downtime, and enhance product quality—all without the need for a complete machine overhaul. With innovative solutions like the Press Kit and Punch Kit, metal fabricators have the tools to transform aging equipment into modern, reliable production workhorses. By choosing a retrofit approach, businesses can secure a competitive edge while safeguarding their investment in legacy machinery.
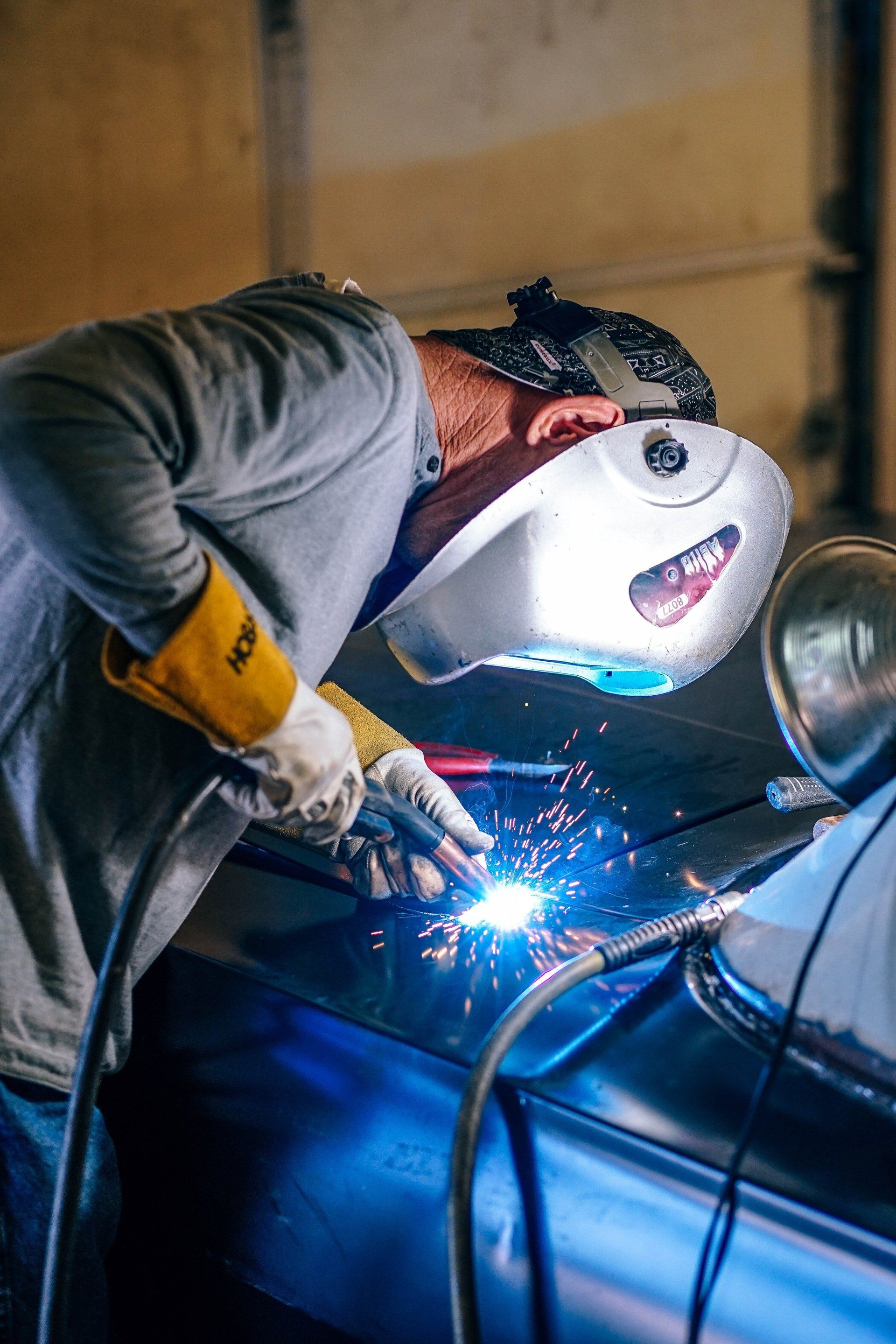
The metal fabrication industry has long relied on CNC machines for precision and reliability. However, many of these machines come equipped with outdated controls that struggle to meet modern production demands. CNC Control Retrofits offer a revolutionary solution—upgrading existing systems to harness the latest technology, improve performance, and reduce operational costs.
The Evolution of CNC Controls
CNC control systems have evolved dramatically over the years. Earlier models were built on legacy technology that is now obsolete, lacking the intuitive interfaces and robust features of modern systems. Upgrading to CNC control retrofits means:
- Integrating PC-Based Technology: This enables more dynamic interfaces and real-time monitoring.
- Accessing Advanced Software: Tools like Bend Wizard, Shear Wizard, and Punch Wizard help operators manage complex operations with ease.
- Boosting Machine Intelligence: Newer control systems can process data faster, allowing for smarter and more efficient production cycles.
Addressing Industry Challenges
Fabricators frequently encounter issues with outdated controls:
- Inconsistent Performance: Older systems can lead to variability in production, affecting both quality and output.
- High Maintenance Needs: Aging electronics often require more frequent repairs, driving up maintenance costs.
- Limited Upgradability: Legacy systems can make it difficult to implement new features or integrate with modern software platforms.
CNC control retrofits directly address these challenges by replacing outdated components with modern, reliable technology that is designed to evolve with industry advancements.
Spotlight on Retrofit Solutions
PC Controls offers a range of products that serve as perfect examples of CNC control retrofits in action:
- Press Kit: Specifically engineered for press brakes, this retrofit solution transforms legacy systems by integrating advanced control mechanisms. This results in improved operational stability and enhanced precision.
- Punch Kit: Tailored for single punches and similar equipment, the Punch Kit brings real-time monitoring and sophisticated diagnostics to older machines. This upgrade minimizes errors and ensures consistent performance.
Benefits for Metal Fabrication Businesses
Implementing CNC control retrofits can lead to significant improvements across various aspects of metal fabrication:
- Enhanced Precision and Accuracy: Modern controls enable finer adjustments, reducing material waste and improving overall quality.
- Operational Flexibility: Upgraded systems offer customizable settings and greater adaptability to different production requirements.
- Streamlined Workflow: Faster processing speeds and intuitive interfaces contribute to smoother, more efficient production cycles.
- Cost Efficiency: By avoiding the need for entirely new machines, businesses can realize substantial cost savings while still achieving high-tech performance.
How to Choose the Right Retrofit Solution
For companies considering a retrofit, several factors should be taken into account:
- Assess Current Machinery: Identify which machines would benefit the most from a control upgrade.
- Determine Production Goals: Understand what improvements are needed, whether it’s increased precision, reduced downtime, or enhanced monitoring capabilities.
- Consult with Experts: Engaging with a company like PC Controls can provide insights into the best retrofit solutions, tailored to your specific machinery and production needs.
Future-Proofing Your Operations
One of the most compelling reasons to invest in CNC control retrofits is the opportunity to future-proof your operations. As technology continues to advance, modern retrofit solutions offer:
- Scalability: Easily upgrade and expand your systems as new features become available.
- Sustained Performance: Maintain high levels of productivity and quality over time without the need for frequent, costly overhauls.
- Enhanced Support: Access ongoing technical support and software updates that keep your machinery operating at its best.
CNC Control Retrofits are not just an upgrade—they’re a revolution in how metal fabrication businesses approach modernization. By investing in solutions like the Press Kit and Punch Kit, companies can seamlessly transform outdated equipment into efficient, modern production tools. These retrofits offer a clear path to enhanced precision, improved workflow, and significant cost savings, ensuring that your business stays at the forefront of the industry. Embracing these upgrades today means preparing your operations for the technological challenges of tomorrow.